PROCESSUS
DE PRÉPARATION
de la cellulose MOULÉe
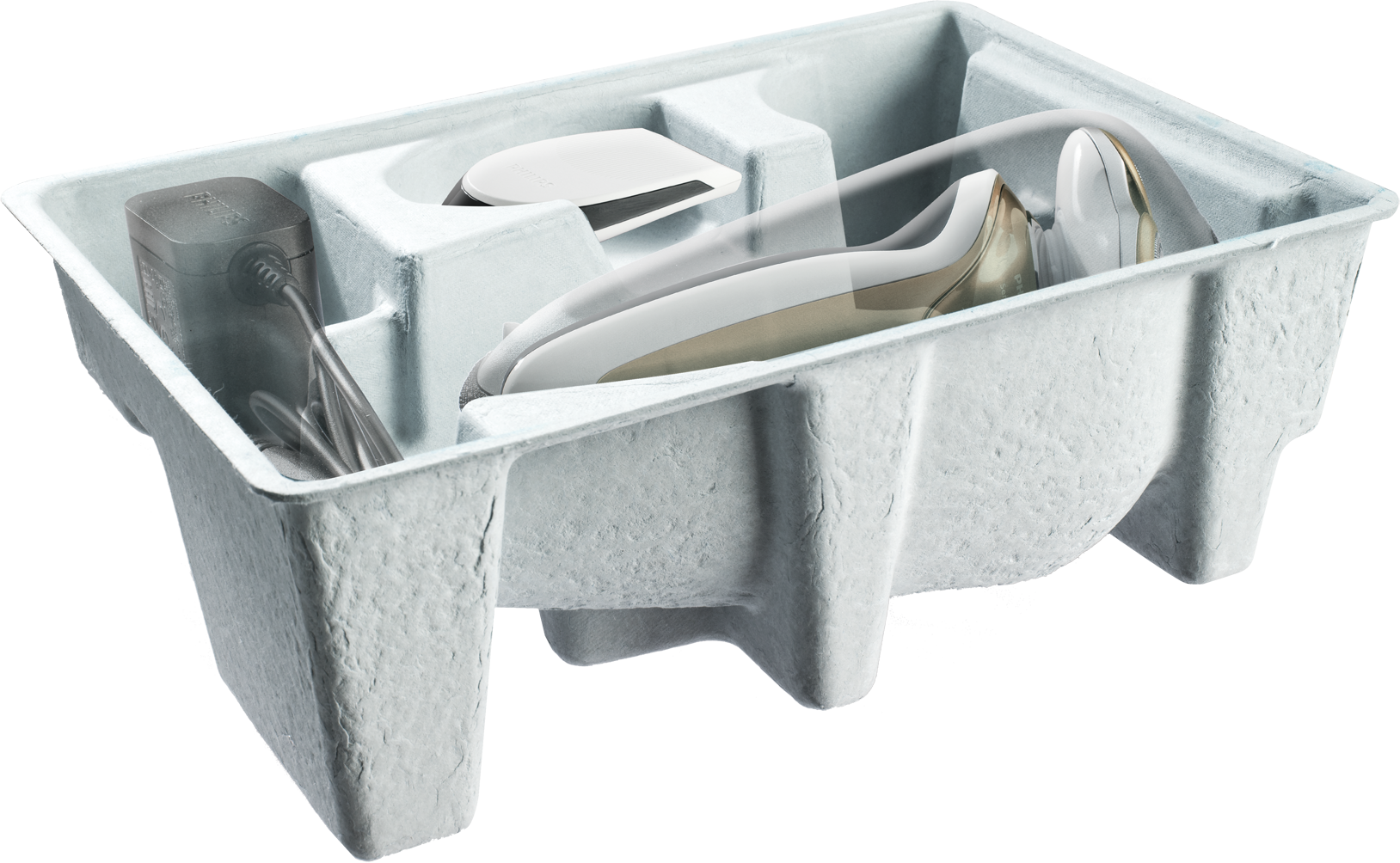
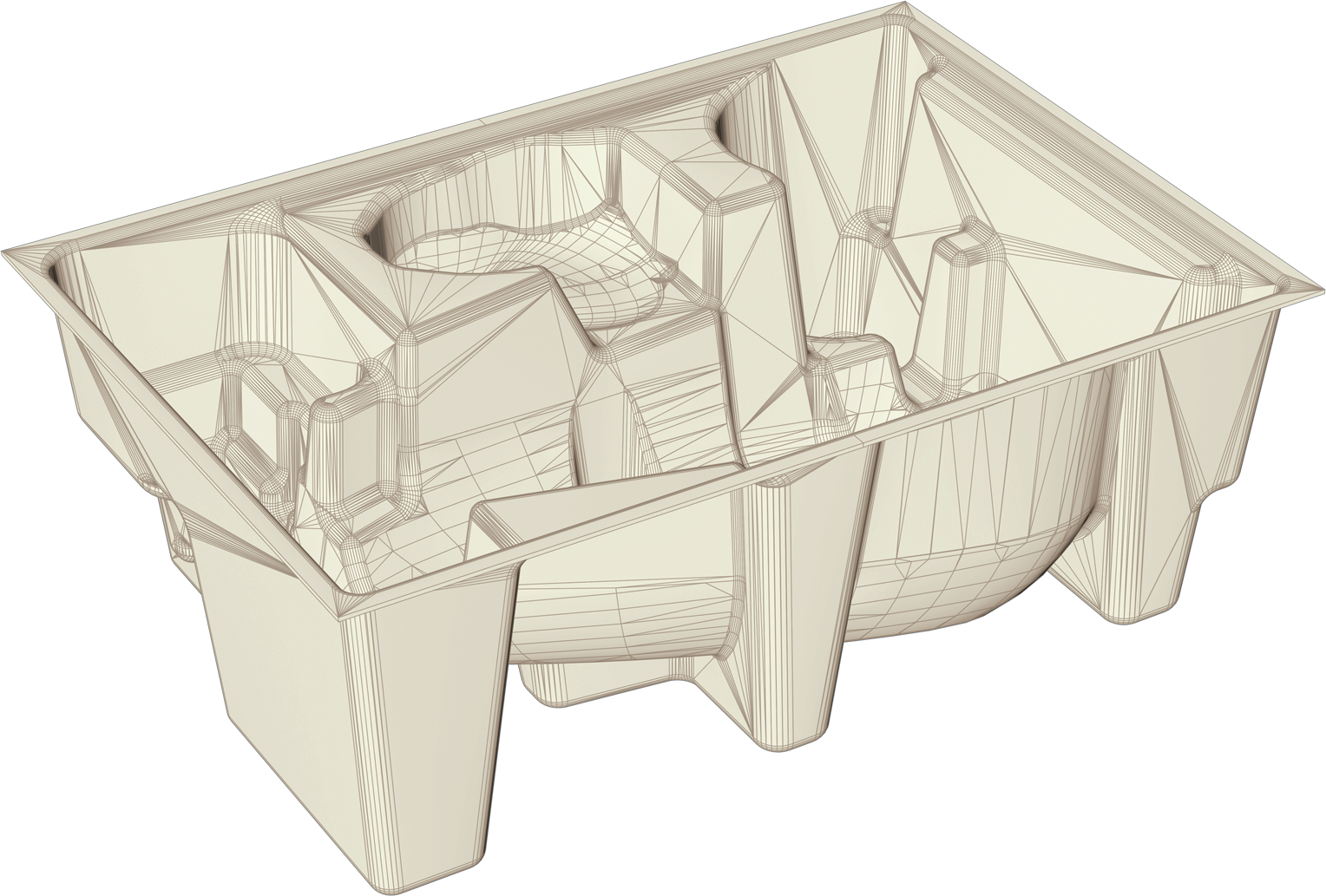
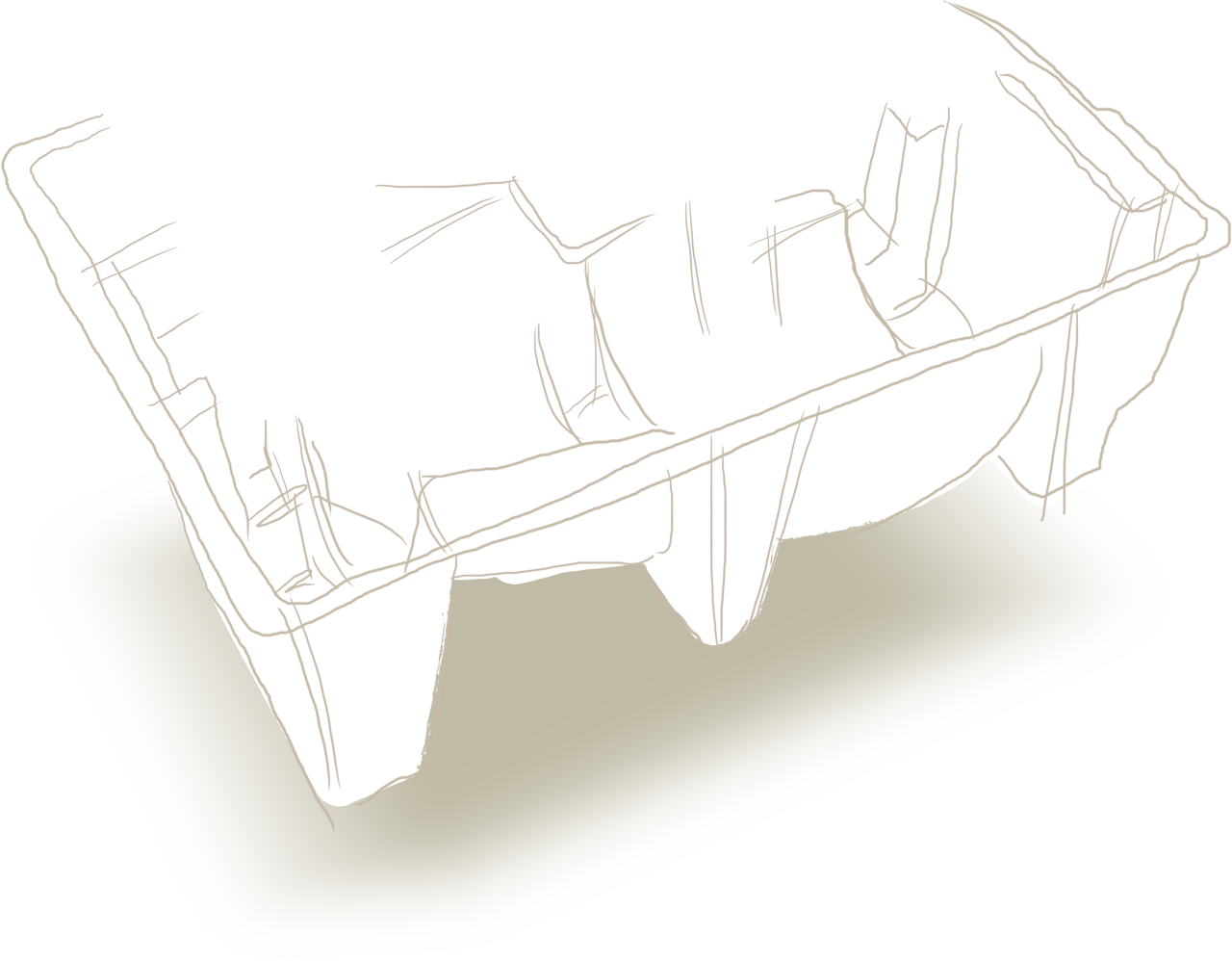
3. Produit final
La dernière étape est la fabrication d’un moule d’échantillonnage qui sera suivie par la production d’un échantillon réel. Les échantillons sont utilisés pour vérifier les formes réelles et pour les essais d’impact. La qualité de la matière utilisée pour réaliser les échantillons est identique à celle de la matière qui servira à la production en masse.
2. Conception 3D
La deuxième étape préparatoire consiste à créer un modèle 3D de grandeur nature. Pour pouvoir réaliser ce modèle 3D, nous avons besoin que le client nous remette des échantillons de produits réels ou des maquettes des produits à emballer.
1. Concept
Une fois que toutes les données d’entrée ont été définies, le calage est rapidement et simplement esquissé. Cette esquisse servira au chiffrage initial et permettra au client de se faire une idée générale de son emballage.
PRODUCTION
PROCESSUS DE PRODUCTION DE LA
CELLULOSE MOULÉE
LIGNE CONVENTIONNELLE
Les vieux papiers collectés (cartons, journaux) sont pesés avec précision et placés ensuite dans un triturateur où ils sont mélangés avec de l’eau pour atteindre une consistance de 7 %. En 15 à 20 minutes, le papier est défibré pour obtenir une pâte qui est pompée au travers d’une filtration en deux étapes. Lors de la première étape, les impuretés lourdes (telles que les petites pierres et le sable) sont séparées ; la deuxième étape de filtration permet de séparer les petits contaminants (le bois, le plastique, le polystyrène et les rubans adhésifs). La pâte nettoyée est stockée dans des cuves avec une consistance résultante de 4 %. La dernière étape de la préparation de la pâte consiste à la mélanger et à la réduire en fonction des paramètres d’exploitation requis. L’ensemble du processus est contrôlé par ordinateur.
Durant la seconde étape de fabrication, la pâte est pompée pour être amenée à la section de formage de la ligne. La pâte y est aspirée dans des moules en aluminium. Une fois l’eau résiduelle aspirée, le produit fini est transporté vers un convoyeur de séchage. Le processus de séchage est surveillé automatiquement ; tout au long de ce processus, l’humidité, la température et la quantité d’air de séchage sont contrôlées. Le temps de séchage du produit se situe entre 25 et 35 minutes en fonction de sa taille et de l’épaisseur du matériau.
Si le client exige un certain niveau de qualité de surface ou une certaine précision dans les dimensions intérieures des cales, les produits seront pressés dans un moule chaud. L’exposition à une température de 180 °C et à une pression de 20 tonnes donnera une surface très lisse au produit. Pour atteindre des dimensions externes précises, les bords du produit sont coupés en fonction des dimensions de la boîte. Les chutes des coupes sont ensuite réutilisées dans le processus de production.
LIGNE THERMOFORMANTE
Pour les produits du thermoformage, nous n’utilisons que des matériaux vierges, sans aucune impureté ni colle. Le matériau d’entrée est pesé avec précision et placé ensuite dans un triturateur où il est mélangé avec de l’eau pour obtenir une consistance de 7 – 8 %. En 15 à 20 minutes, la matière est défibrée et se transforme en pâte. Une fois nettoyée, la pâte est stockée dans des cuves en acier inoxydable avec une consistance résultante de 2 %. La dernière étape de la préparation de la pâte consiste à la mélanger et à la réduire en fonction des paramètres d’exploitation requis. L’ensemble du processus est contrôlé par ordinateur .
Durant la seconde étape de fabrication, la pâte est pompée pour être amenée à la section de formage de la ligne. La pâte y est aspirée sur des moules en aluminium. Une fois l’eau résiduelle aspirée, le produit fini est transporté vers des moules de pressage chauds. Durant le processus de séchage, les calages, encore humides, sont compressés à haute pression. La température des moules est automatiquement régulée entre 150 et 220 °C. Le temps de séchage du produit se situe entre 60 et 110 secondes en fonction de sa taille et du poids des calages.
Si le client exige des dimensions extérieures précises, les bords du produit seront coupés en fonction des dimensions de la boîte. Les chutes des coupes seront ensuite réutilisées dans le processus de production.